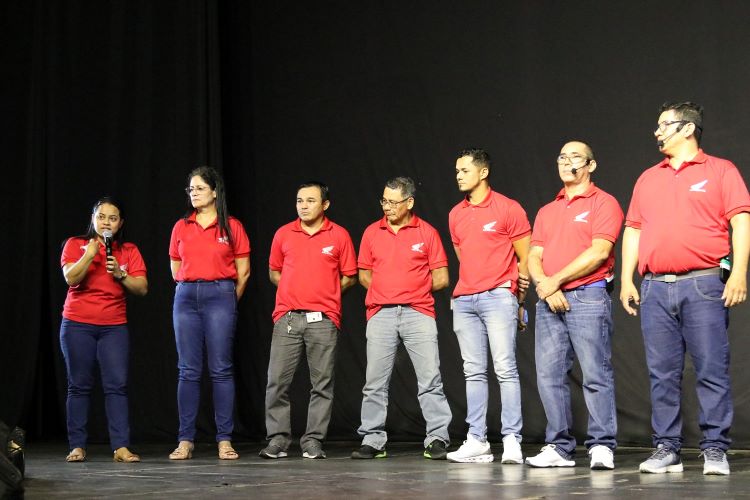
Colaboradores da Yamaha Motor da Amazônia Ltda marcaram presença ontem na 24ª Mostra de Melhorias para a Qualidade, no Studio 5, para apresentação de seus projetos que concorrem na modalidade Processo ao Prêmio Qualidade Amazonas 2023, a exemplo do projeto “Combinando técnicas inovadoras e soluções tecnológicas avançadas sustentáveis, buscando aprimorar a eficiência e a durabilidade do tanque de combustível, garantindo uma soldagem precisa e de alta qualidade”. Do mesmo grupo, a Yamaha Motor Componentes da Amazônia, descreveu o “Aumento da capacidade produtiva na Unidade Ferroso II”. A feira ocorre até às 17h30 desta sexta-feira, 19.
Equipe da Yamaha Motor da Amazônia criou uma máquina que resolve quatro problemas que a fábrica enfrentava até 2022. Segundo Armando Neto, especialista industrial, antes o operador precisava segurar a peça a ser soldada, a alimentação de peças era demorada e falhava, havia ausência de controle e monitoramento de temperatura, além de dificuldade em visualizar e monitorar a pressão. Como ação para solucionar essas dificuldades, a equipe de especialistas da produção criou um equipamento de soldagem de movimentação em dois eixos, com alimentação de peça automática, inclusão de chiller para controle e monitoramento de temperatura e inclusão de sistema controlador digital de pressão, onde não há mais manuseio humano.
O investimento de R$ 330 mil no projeto já rendeu R$ 813.634,16 para a empresa em dois anos, desde a sua implantação, e um saving de R$ 483.634, além da redução de 33,82% no consumo de energia. Segundo o especialista industrial, Raphael Ferreira, como ganhos secundários, a empresa ganhou a satisfação dos colaboradores e o fortalecimento da imagem da organização e de seus produtos.
De acordo com o analista de engenharia industrial da Yamaha Motor Componentes da Amazônia, Carlos André Migliorin, a Unidade Ferroso II tinha como meta aumentar sua capacidade na linha de eixo retífica de eixos em 30% até dezembro de 2022, tendo como lucro +110%, o equivalente a R$ 176.995,00, em cima do investimento realizado de R$ 159.808,00 e conseguiu atingir em 2023 muito além do esperado, 240%, lucrando um valor de R$ 425.395,00.
“Como eliminar batida na capa traseira do modelo K1S” desafiou a equipe da Yamaha Motor da Amazônia, representada pelo analista técnico, Kayson Isaac Sahdo, e o operador de máquina, Wagner Gonçalves. Realizado em 2022, o trabalho investigou na cadeia produtiva, do setor cliente ao setor de origem, onde estava o problema que gerava para a empresa despesa em recuperação de cada peça batida, valor de R$ 27.659,56, sendo R$ 20.655,44 de repintura, R$ 6.048,90 de ar comprimido utilizado e R$ 955,22 em repintura.
Sahdo e Gonçalves explicaram o exame minucioso nos dois equipamentos utilizados no processo da capa traseira. O primeiro a ser analisado foi a prensa comando simples (110T SC), que corta, dobra e modela materiais, comprimindo itens grandes em blocos reduzidos com a dependência operacional para funcionamento do ciclo da peça. Após avaliação, com a separação e inspeção por duas vezes em 100% de 600 peças produzidas na máquina, foi encontrado zero de batidas.
O segundo equipamento, prensa automática (110T AUT) que corta, dobra e modela materiais, comprimindo itens grandes em blocos reduzidos que não dependem diretamente do colaborador para funcionamento do ciclo da peça. Na etapa, o fluxo foi avaliado com a inspeção de duas mil peças produzidas no processo 110T automática e encontradas 1.860 peças batidas, e localizado o problema no processo.
O grupo de trabalho responsável pela qualidade da empresa utilizou o diagrama de 4W’s para confirmar o problema e constatou que a falha na implantação da peça contribuía para a ocorrência de batida. Sendo assim, por meio de brainstorms, desenvolveu três propostas para reduzir ou mesmo zerar as batidas. A última, que chegou a reduzir a zero as batidas, alterou o método de saída da peça e a forma de armazenamento, eliminando o uso de ar comprimido, saída de peça por gravidade pela parte frontal da máquina e utilização de basquet marfinite para armazenamento organizado. Foram produzidas 3.600 peças, sem nenhuma batida.
Para manter o projeto iniciado em 2022, além dos documentos de validação do projeto emitido ou revisado e o treinamento com os colaboradores, a equipe de trabalho, junto ao grupo de novos modelos, incluiu no manual setorial que seja considerada a melhoria na extração da peça, observando melhor posicionamento do colaborador para inspeção da peça, além de problemas de qualidade futuros, similares aos batidos encontrados no processo da capa traseira do K1S.
“Além da meta atingida, a segurança também foi alcançada com a eliminação do risco de acidente na recuperação da peça e com a redução do ruído na produção da peça, eliminando o sopro por ar comprimido na máquina 110T”, disse Gonçalves. Para a equipe, a melhoria em custo para a empresa foi o valor que se gastava para recuperar uma peça, mas também contribuiu com o meio ambiente e na garantia da alegria de se trabalhar em toda a cadeia produtiva.